
By measuring both the density and dynamic viscosity the kinematic viscosity can be calculated. The damping of the resonator can be used to measure dynamic viscosity. Results for density measurements made with a microtube have been published previously. As can be seen by the expression above, the density is inversely proportional to the square of the resonance frequency. Where vV is the internal volume of the resonant tube, mt is tube mass, K, is the spring constant of the tube and f is the resonance frequency of the tube. The density of a liquid p is given by the expression: Where the n is dynamic viscosity (cP or mPa s) and p is the density (g/cm3) of the fluid. The kinematic viscosity u (cSt or mm2/s) of a fluid is given by the expression:
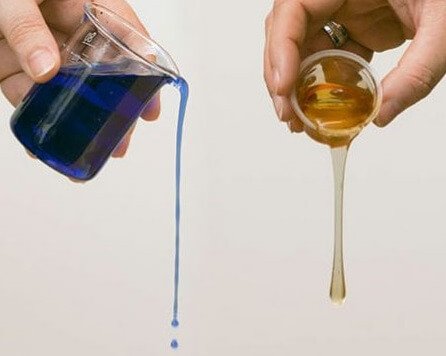
This paper will show that a res-onating microtube can be used to measure both the density and viscosity of a fluid. 1 shows a photograph of such a microtube. Micromachined resonating tubes have been used to measure mass flow, density and chemical concentration. Several small standing acoustic wave (SAW) and microelectromechanical systems (MEMS) viscometers have been developed in recent years. Viscosity measurements have been made using capillary force, falling balls, moving paddles and vibrating tuning forks. The measure-ment of viscosity has been employed for many decades to monitor and test lubricants, blood, mucus, adhesives, paints, fuels and other fluids. The viscosity of a fluid is often represented as a coefficient, which describes the diffusion of momentum in the fluid. Viscosity is often thought of as the fluid’s friction, resistance to flow or the fluid’s resistance to shear when the fluid is in motion. A variety of applications for the sensor will be discussed. The dynamic viscosity measurement error between the new sensor and the calibration references ranges from 0.006 to 0.15 cP, or 0.6 to 8%. The density is measured via the change in resonant frequency caused by a change in fluid density while the viscosity is measured by monitoring the peak signal of the resonator. Fluid damping requires a change in drive voltage to maintain a constant vibrational amplitude. Dynamic viscosity is measured using the damping effect that a fluid has on the motion of the resonating tube. Abstract This article examines the use of a micromachined resonating tube to measure both the dynamic viscosity and density of a fluid enabling the calculation of the kinematic viscosity.
